Case Study 1
Reducing Inspection Times for a Major Automobile Manufacturer
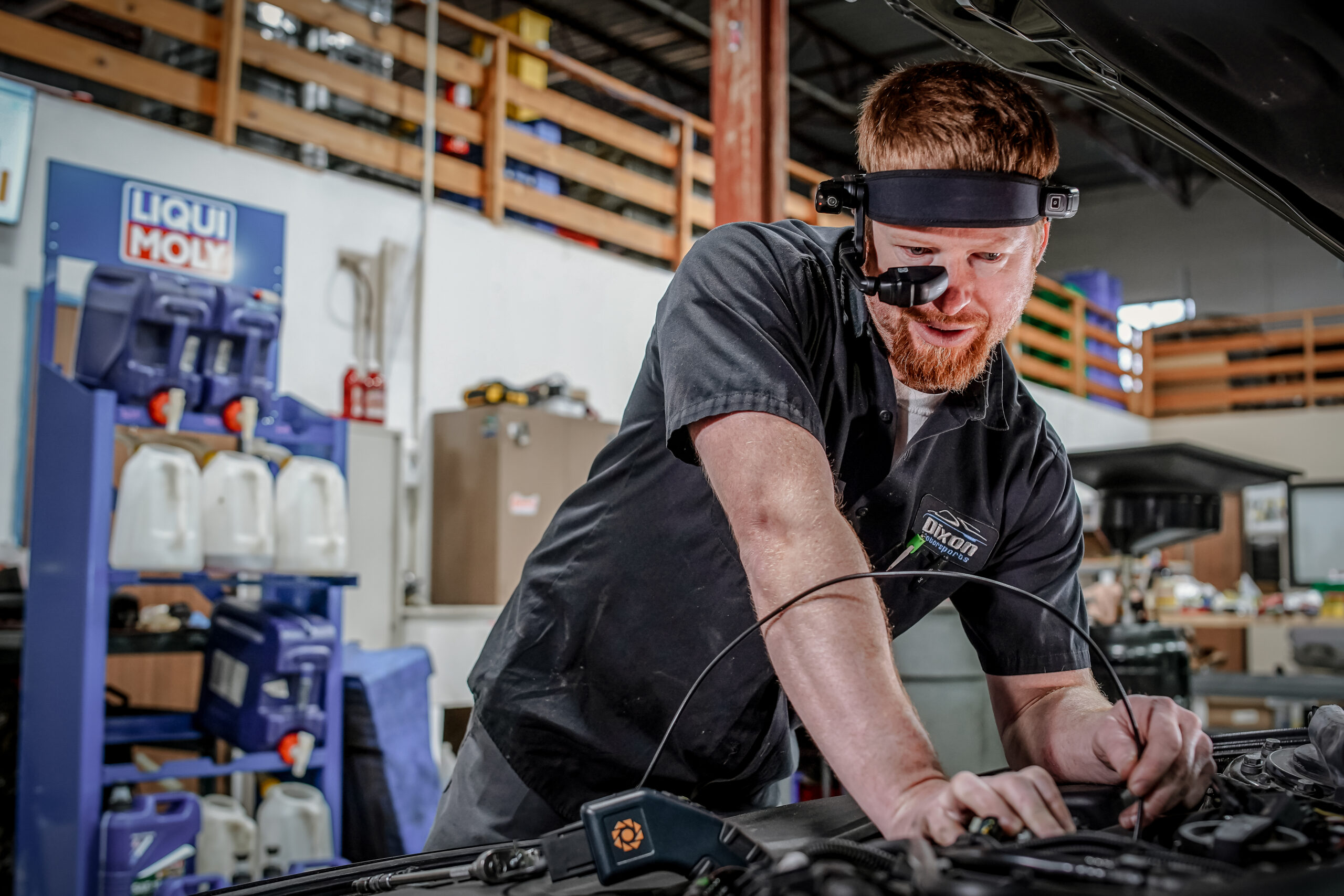
Reducing Inspection Times for a Major Automobile Manufacturer
The Problem
A top multinational automobile and commercial vehicle manufacturer faced a significant challenge with a windshield wiper blade recall. The existing inspection process required technicians to use a cumbersome mirror on a stick to identify the part numbers on windshield wiper blades. This method was not only labor-intensive but also inefficient, as it required 30 minutes of disassembly and reassembly to access the part number label.
This manual process resulted in additional workload and reduced productivity, burdening technicians and increasing labor costs.
The Solution
Inspectron introduced the WiScope, a tool designed for quick and easy access to difficult-to-reach areas of the vehicle. By using the WiScope, technicians could photograph the part number directly, bypassing the need for extensive disassembly. This streamlined the process, allowing technicians to quickly determine if remedial action was required.
Results
The implementation of the WiScope provided substantial time savings. Each inspection job was reduced by 20 minutes, resulting in significant labor hour savings over the course of the recall project.
Total Project Labor Hours Saved: 60 hours
Additionally, the WiScope offered several tangible benefits:
Streamlining Field Service Inspections for a Global Oil and Gas Company
The Problem
A globally recognized oil and gas company sought to enhance their field service inspections process. The creation of 30+ page reports required up to 40 hours of preparation time per machine. This extensive workload consumed a significant portion of a technician’s time.
The Solution
Inspectron’s products formed part an integrated solution that included the WiScope, WiTorch, WiCloud, an Android tablet, and workflow software. This system allowed technicians to efficiently navigate through the workflow process, capturing images and videos in real-time. The media was automatically inserted into the correct places within the report as the inspection took place.
This innovative approach eliminated the need to retrospectively find and insert the correct images after completing the inspection, thus removing hours from the process.
Results
The implementation of Inspectron’s solution led to remarkable improvements:
Accelerating Warranty Repair Order Approvals for a Top Sports Car Manufacturer
The Problem
This world leading leading sports car manufacturer faced significant challenges in optimizing the approval times for Warranty Repair Orders. The existing process was slow, with multiple exchanges between technicians and technical assistance centers, causing delays. Additionally, the clarity of borescope images shared on Microsoft Teams calls needed improvement to ensure accurate diagnostics and faster approvals.
The Solution
Inspectron tools formed part of a cutting-edge solution by connecting the WiScope to HoloLens 2, allowing technicians to share the WiScope camera feed live during Microsoft Teams calls. This setup enabled real-time screen sharing, facilitating immediate RO approvals. The key benefits included:
Accelerated Approval Time: Approval time was improved by four times.
Reduced Ticket Exchanges: The number of message exchanges between technicians and technical assistance centers was reduced, saving multiple hours of back-and-forth communication.
Enhanced Image Quality: HD image quality improved diagnostic confidence.
User Flexibility: The tools were compatible with other Windows devices, offering flexibility for users.
Ease of Use: Images and videos could be saved directly to the device for easy access and record-keeping.
Results
The implementation of Inspectron’s solution led to several tangible benefits:
Faster Approvals: The immediate RO approval process significantly reduced downtime.
Improved Efficiency: The reduction in message exchanges and quicker diagnosis allowed technicians to focus on more critical tasks.
Increased Customer Satisfaction: The ability to get vehicles back on the road faster improved overall customer satisfaction, a top priority for the manufacturer.